The power of digital twins: Improving productivity and maintenance in manufacturing
EPA System / News & Eventi
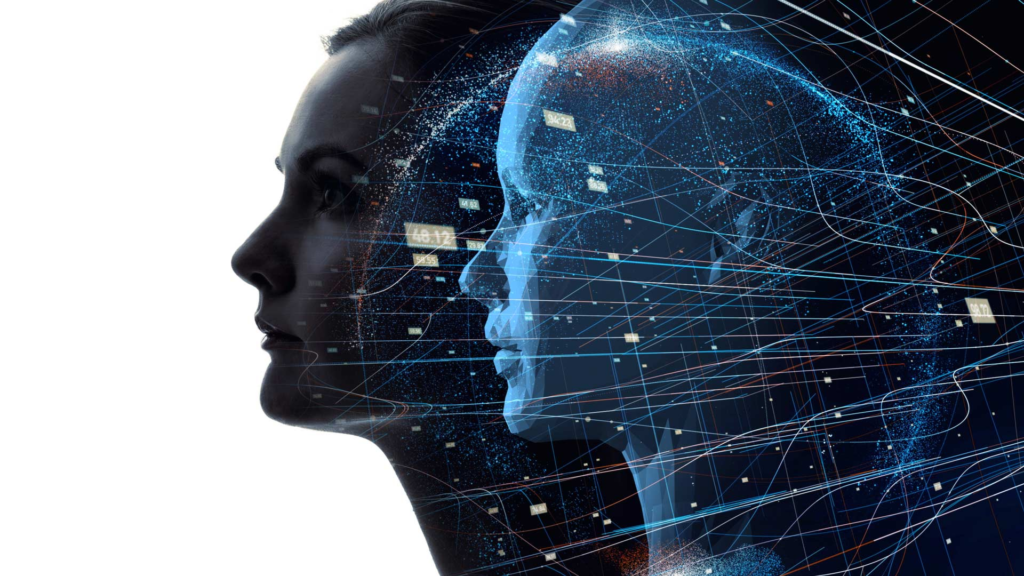
What are digital twins and how do they work?
Digital twins are precise virtual representations of products, processes, or physical systems in the real world. Using real-time data and sophisticated algorithms, digital twins can simulate the behavior and performance of a physical object. This allows operators and decision-makers to monitor, analyze, and optimize manufacturing operations in a secure virtual environment.
Digital twins operate by collecting data from sensors and connected devices within a factory. These data are then used to create a digital replica of a specific product or process. Through the use of advanced analysis algorithms, digital twins can simulate the operation of an object or system under various conditions, providing in-depth information on performance and areas for improvement.
Advantages of using digital twins in the manufacturing sector
The use of digital twins in the manufacturing sector offers several significant advantages. Firstly, digital twins enable detailed analysis and simulations in a virtual environment, reducing the need for expensive physical tests and decreasing product development time. This leads to improved productivity and overall operational efficiency.
Furthermore, digital twins allow real-time monitoring of plant and production process performance, enabling quick interventions in case of anomalies or malfunctions. This helps reduce machine downtime and optimize preventive maintenance, ultimately reducing overall maintenance costs.
Lastly, digital twins also offer the opportunity to enhance collaboration among design, production, and maintenance teams. With an accurate digital replica available, different teams can work more effectively, sharing information and making decisions based on shared data.
Use cases of digital twins to enhance productivity
Digital twins offer multiple use cases to improve productivity in the manufacturing sector. For example, they can be used to optimize the layout of production lines by identifying critical points and reducing setup times. Additionally, digital twins can simulate and test new production processes, allowing the identification of potential issues and making adjustments before implementing new physical production lines.
Another significant use case for digital twins is simulating material flow and logistics operations. By using a digital twin, it’s possible to analyze and optimize the movement of materials within a factory, identifying possible congestions or inefficiencies and proposing appropriate solutions.
Lastly, digital twins can be used to improve the energy efficiency of manufacturing operations. By monitoring and analyzing energy consumption data, digital twins can identify areas of waste and suggest changes to reduce energy use and improve overall sustainability.
Use cases of digital twins in maintenance and predictive analysis
In addition to improving productivity, digital twins can play a crucial role in maintenance and predictive analysis in the manufacturing sector. Using data from sensors and monitoring equipment, digital twins can predict machine or component failures, allowing timely planning of preventive maintenance.
A common use case of digital twins in maintenance is fault diagnosis. Digital twins can analyze sensor data to identify signs of malfunction or deterioration, enabling intervention before the problem manifests. This reduces machine downtime and avoids costly sudden failures.
Moreover, digital twins can be used to optimize the maintenance process by monitoring machine performance and suggesting maintenance interventions based on actual conditions. This helps reduce maintenance costs, optimize resource utilization, and extend the lifespan of facilities.
Implementation of digital twins in production
Implementing digital twins in production requires several key steps. Firstly, it’s necessary to identify critical areas where the use of digital twins can bring the most benefits. This may include designing new products, optimizing existing production lines, or preventive maintenance of machines.
Next, it’s essential to gather the necessary data to create the digital twin. This data can come from existing sensors or may require the installation of new monitoring devices. It’s crucial to ensure that the collected data is accurate and representative of the real physical system.
Once the data is collected, the digital twin can be created using specialized software and algorithms. This requires expertise in data analysis and system modeling. It’s also important to ensure that the digital twin is constantly updated with real-time data to maintain an accurate representation of the physical system.
Finally, it’s necessary to integrate the digital twin into the daily operations of the company. This may involve training staff and adopting new processes and procedures. Involving all levels of the organization is crucial to ensure proper implementation and maximize the benefits of digital twins.
Challenges and considerations for adopting digital twins
Despite the numerous advantages offered by digital twins, there are also challenges and considerations to take into account when adopting this technology in the manufacturing sector. One of the main obstacles is the collection of accurate and representative data from the physical system. This may require the installation of new sensors and monitoring devices, as well as collaboration with external suppliers and partners.
Another challenge is data management. Digital twins generate a large amount of data that needs to be collected, stored, and analyzed efficiently. This requires the adoption of robust IT infrastructure and staff training to make the best use of data analysis tools.
Additionally, the implementation of digital twins requires a significant investment in terms of financial and human resources. Time and resources must be dedicated to creating and maintaining digital twins, as well as training staff on the use of this technology.
Finally, it’s important to consider data security. Digital twins may contain sensitive information about manufacturing operations and products. It’s essential to implement adequate security measures to protect data and prevent unauthorized access.
Tools and technologies for creating digital twins
To create precise and reliable digital twins, various specialized technologies and tools are available. One of the most common tools is modeling and simulation software, which allows the creation of a digital replica of a specific object or process. These software applications use sophisticated algorithms to analyze data and simulate the behavior of the system.
Additionally, sensors and monitoring devices play a crucial role in creating digital twins. These devices collect real-time data on key system parameters, enabling the creation of an accurate digital replica.
Other tools and technologies used to create digital twins include virtual and augmented reality, allowing operators to interact with the digital twin intuitively and realistically. Furthermore, artificial intelligence and machine learning are used to analyze data and improve the performance of digital twins over time.
Trends and future advances of digital twins
Digital twins are becoming increasingly widespread in the manufacturing sector, and they are expected to continue evolving and improving over time. One emerging trend is the interconnection of digital twins to create a network of interconnected systems. This will enable greater collaboration among different actors within the manufacturing ecosystem, optimizing operations and improving overall efficiency.
Another significant trend is the use of digital twins in the Internet of Things (IoT) context. With the increasing number of connected devices within a factory, digital twins will be able to acquire real-time data from a wide range of sources, allowing more in-depth analysis and data-driven decisions.
Finally, it is expected that digital twins will become increasingly autonomous and intelligent over time. The integration of artificial intelligence and machine learning will allow digital twins to analyze data autonomously and make real-time decisions without human intervention.
The future of manufacturing with digital twins
The manufacturing industry is undergoing an unprecedented transformation thanks to the adoption of digital twins. This innovative technology offers enormous potential to improve productivity and maintenance in the sector, optimizing operations, predicting machine failures, and enhancing overall efficiency.
Despite the challenges and considerations associated with implementing digital twins, their positive impact is undeniable. With the evolution of technologies and the integration of best practices, digital twins will continue to drive innovation in the manufacturing sector and create new opportunities for companies aiming to remain competitive in the global market.